Wysoka dostępność części dla przemysłu stoczniowego
Już na początku XX wieku fabryka Brunvoll Motorfabrik wyprodukowała pierwsze silniki wysokoprężne i śruby napędowe do łodzi rybackich. Podążając za pomysłem braci Gjendemsjø, dwóch lokalnych rybaków, firma rozpoczęła rozwój i produkcję strumieniowych sterów tunelowych w 1964 roku – nadal jest to powszechna zasada napędu morskiego.
Dzisiejsza Grupa Brunvoll, z siedzibą w Molde w Norwegii, jest bardziej niż kiedykolwiek kojarzona z potężnymi morskimi systemami napędowymi, niezawodnymi przekładniami i innowacyjnymi elektronicznymi układami sterowania. Około 520 pracowników w pięciu zakładach produkcyjnych zapewnia płynne procesy od rozwoju przez produkcję aż po serwis.
Innowacyjne układy napędowe do statków o żywotności ponad 25 lat
Od łodzi rybackich po statki wycieczkowe – systemy napędowe i sterowania firmy Brunvoll używane są na całym świecie. „Obecnie w użyciu jest ponad 10 000 jednostek” – Magne Gøran Lyngstad, wiceprezes ds. procesów i inżynierii produkcji, ilustruje szerokie zastosowanie ważnych komponentów statku. 75 procent produkcji jest przeznaczone na eksport, a asortyment produktów jest stale rozwijany. „Każdego roku 70 000 godzin poświęcamy na opracowywanie innowacji”. Niezawodność systemów napędowych jest tak wysoka, że ich żywotność przekracza żywotność statków. „Ponad 25 lat to tutaj powszechne zjawisko” – dodaje Kjetil Hoem, kierownik ds. projektów inwestycyjnych. Tak więc, oprócz rozwoju i produkcji – które są prawie w całości wykonywane we własnym zakresie – w firmie Brunvoll bardzo ważny jest również serwis.
Dwie bezzałogowe zmiany dziennie dzięki inteligentnym zautomatyzowanym rozwiązaniom
„Gwarantujemy wysoką dostępność części zamiennych, ponieważ krótki czas reakcji ma kluczowe znaczenie” – wyjaśnia wysoką gotowość serwisową Kjetil Hoem. „Nasza szeroka gama produktów wymaga ogromnej różnorodności części, od małych do dużych. W większości przypadków mówimy o partiach do 15 sztuk”. Wymaga to zatem wysokiego stopnia elastyczności ze strony działu produkcji. Magne Gøran Lyngstad wskazuje rozwiązanie: „Dzięki inteligentnym zautomatyzowanym rozwiązaniom możemy oprócz zwykłej zmiany roboczej wykorzystywać dwie bezzałogowe zmiany dziennie i znacznie zwiększyć naszą wydajność”. Do tej pory zakład w Brunvoll automatyzował głównie centra obróbcze i centra tokarsko-frezarskie. „Ostatnia inwestycja była pierwszą, która objęła obszar złożonych części toczonych”. Tutaj właśnie DMG MORI wkracza do gry.
Zautomatyzowana 6-stronna kompletna obróbka z systemem Vision
Zautomatyzowane rozwiązanie producenta obrabiarek opiera się na modułowym systemie MATRIS i obejmuje obrabiarkę NTX 3000, system przenośników dla europalet oraz robota FANUC z automatyczną zmianą chwytaków. W celi mieści się siedem chwytaków. Za pomocą systemu 3D Vision robot pobiera elementy z europalet i mocuje je w obrabiarce. Schowek umożliwia mu przenoszenie obrabianych przedmiotów. Gotowe części są wyjmowane, czyszczone w stacji myjącej i umieszczane z powrotem na paletach. „W zależności od rozmiaru elementu, możemy załadować elementy na palety na kilku poziomach za pomocą drewnianych półek. W tym przypadku robot obsługuje również te poziomy” – mówi Kjetil Hoem. Cały proces jest kontrolowany przez przyjazne dla użytkownika sterowanie MAPPS. Cały system jest również przygotowany do korzystania z autonomicznych pojazdów transportowych (AGV), których Brunvoll planuje używać w przyszłości do dostarczania i odbierania palet.
NTX 3000: wydajna obróbka tokarskofrezarska z momentem obrotowym 130 Nm
Firma Brunvoll wybrała obrabiarkę NTX 3000 do obróbki detali o średnicy od 45 do 400 mm. Maksymalna długość części o wadze do 120 kg wynosi 400 mm. Wszechstronne centrum tokarsko-frezarskie zapewnia również kompletną obróbkę 6-stronną, nawet złożonych komponentów. Ponadto, dzięki mocnemu wrzecionu tokarskfrezarskiemu compactMASTER o momencie obrotowym ponad 130 Nm, możliwe jest wykonywanie operacji frezarskich jak na centrum frezarskim. Stosowane narzędzia są wyposażone w chip Balluff, dzięki czemu do obrabiarki zawsze wczytywane są prawidłowe dane narzędzia.
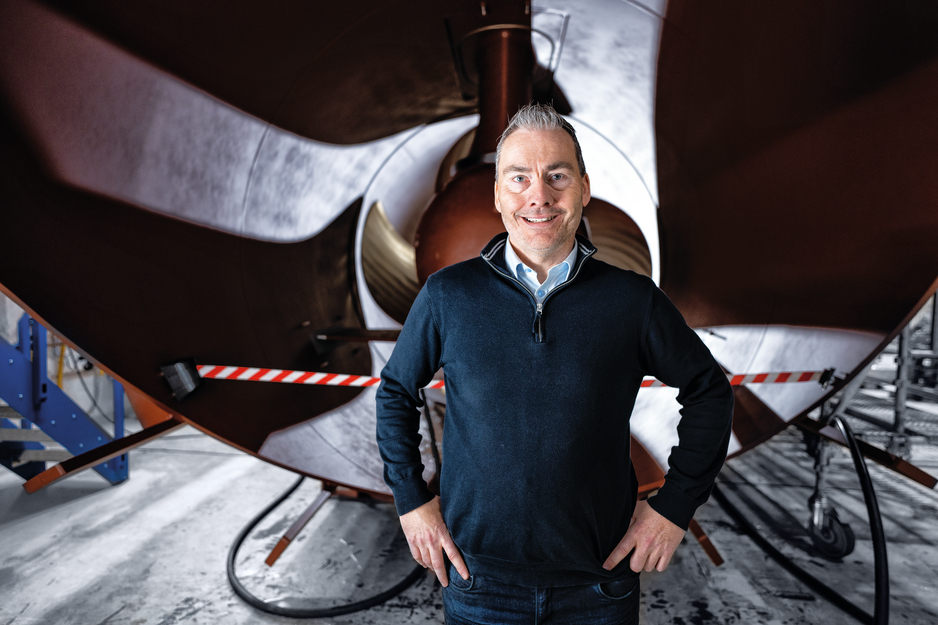
Maksymalna elastyczność dzięki automatycznej wymianie szczęk mocujących
Bardzo zróżnicowane detale wymagają również bardzo różnych systemów mocowania.„W przypadku tego rozwiązania produkcyjnego istotne było, aby robot mógł również zmieniać szczęki mocujące” – mówi Magne Gøran Lyngstad, opisując jedno z wyzwań. W tym celu DMG MORI wyposażyła go w specjalny chwytak i zintegrowała z celą i systemem regałów z miejscem na 60 zestawów szczęk zaciskowych po trzy szczęki każdy. Za pośrednictwem obszaru podawania robot może pobierać szczęki zaciskowe do komory robota i przechowywać je lub natychmiast zamontować. System zaciskowy opracowany przez partnera DMQP (DMG MORI Qualified Products) firmę Schunk jest zaprojektowany do takiej automatycznej zmiany. Układy mocowania, takie jak chwytaki i palety, są identyfikowane za pomocą systemu RFID, aby zapewnić absolutną niezawodność procesu. Fakt, że firma Brunvoll zleciła DMG MORI zaprojektowanie i instalację zautomatyzowanego rozwiązania był częściowo spowodowany tym, że wszystko pochodziło z jednego źródła – z jedną osobą kontaktową, która koordynowała wszystkie operacje. Z drugiej strony istotnym punktem była cena zakupu. Zespół w Japonii był odpowiedzialny za zaprojektowanie rozwiązania produkcyjnego. „Przeprowadziliśmy tam również wstępną akceptację, aby ułatwić późniejsze wprowadzenie ulepszeń” – wspomina Kjetil Hoem. Od czasu końcowej instalacji w Molde, zautomatyzowana obrabiarka NTX 3000 jest więcej niż niezawodna.
System automatyzacji umożliwia większe skupienie się na badaniach i lepszą obsługę
Zwiększenie wydajności dzięki bezzałogowej produkcji w nocy i w weekendy to tylko jeden z argumentów przemawiających za tym, by firma Brunvoll koncentrowała się bardziej na zautomatyzowanych systemach produkcyjnych. „Fakt, że wprowadzamy tę koncepcję toczenia, rekompensuje również niedobór wykwalifikowanych pracowników i wąskie gardła kadrowe” – wyjaśnia Magne Gøran Lyngstad zastosowanie takich roz- wiązań. „Wykorzystujemy potencjał naszych dobrze wyszkolonych pracowników do badań i usług, a nie do stosunkowo prostych operacji uzbrajania obrabiarek”. Mimo, że firma Brunvoll ma obecnie 40 młodszych pracowników, z pomocą coraz bardziej autonomicznej produkcji możliwe jest bardziej niezależne i elastyczne planowanie. „Rozwiązania z zakresu automatyzacji pomagają nam zachować konkurencyjność i rozwijać się w sposób zrównoważony”.
BRUNVOLL AS
- Firma założona w 1912 r. w Harøya w Norwegii, produkuje silniki wysokoprężne i śmigła, a od 1918 r. działa w zakładzie w Molde.
- 1964 Rozwój i produkcja innowacyjnych napędów tunelowych.
- 5 zakładów w Norwegii zatrudniających ponad 500 pracowników do produkcji układów napędowych dla statków, w tym systemów sterowania i automatyzacji.
Skontaktuj się z nami w sprawie technicznych materiałów prasowych DMG MORI.